How to safely carry out an electrical panel inspection
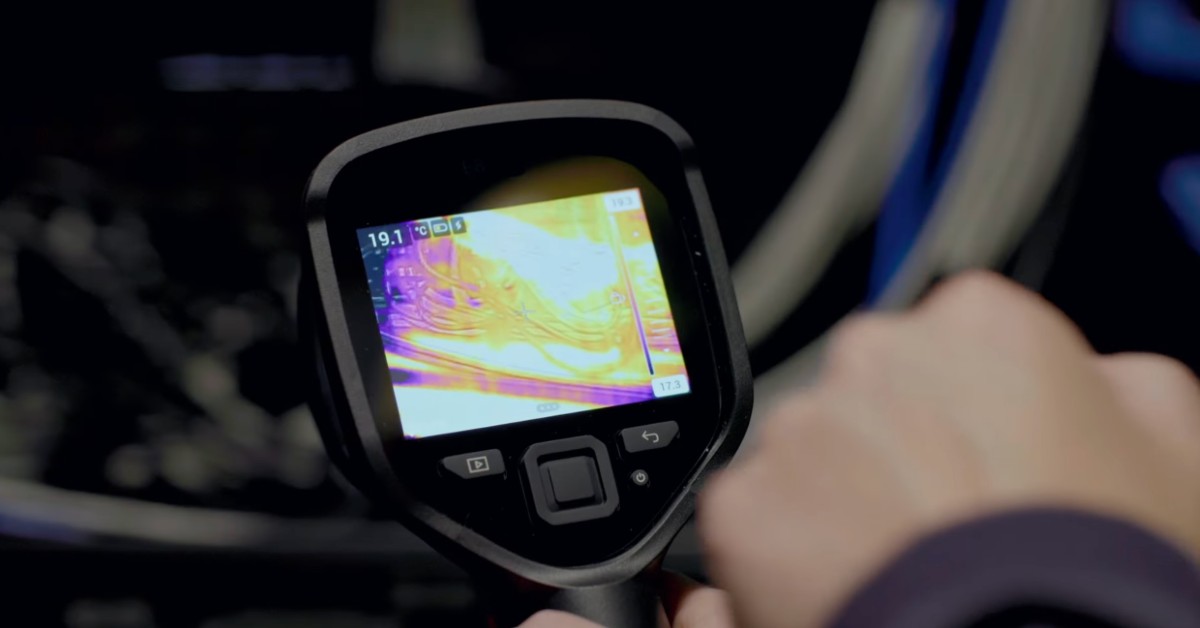
Electrical injuries carry a disproportionately high fatality rate. They are the leading cause of workplace fatalities, accounting for one-fifth of all exposure-related deaths in 2020 (NIOSH, 2020).
Clearly, when it comes to handling sensitive electrical components, there is no room for complacency.
These energy-intensive environments can be dangerous when mismanaged, and even the most seemingly routine of actions can take a fatal turn. In this guide, we'll delve into the essential steps for conducting a safe electrical panel inspection with an at-a-glance checklist to keep you on track.
Understanding the importance of electrical inspections
Manufacturing is one of the world’s most dangerous industries. It’s the second most fatal sector in the UK, according to data from the Health & Safety Executive, with over 1000 injuries every year reported to the HSE.
For industrial engineers and operators, ensuring the safety of electrical systems within your facility is vital. Electrical inspections play a crucial role in identifying potential hazards before they can impact production. Unplanned downtime and emergency maintenance are, after all, very costly - both in terms of labour and knock-on production line losses.
Globally, the scale of electricity usage in industrial facilities is immense. In the US alone, it accounts for a third of all energy consumption (US EIA, 2022). Clearly, for such a critical commodity to industry, downtime is far from ideal - so regular electrical inspections are an important part of ensuring business continuity.
However, electrical inspections are not just about compliance; they are about safeguarding lives, property, and the smooth, continuous operation of industrial processes. By conducting thorough inspections, industrial engineers can identify risks, prevent accidents, and ensure the longevity of equipment.
But despite the electrical industry experiencing over a third fewer accidents in 2020 than in 1980 (NIOSH, BLS, 2020), the inherent danger is no less.
Complacency kills, so electrical engineers must remain vigilant - even in the most routine of inspections. That is why, perhaps somewhat counterintuitively, physically inspecting the unit is the final step of any electrical panel inspection. First, operators must:
Identify all potential hazards in the environment
Before commencing any electrical inspection, it's crucial to conduct a comprehensive risk assessment of the environment. Identify potential hazards such as exposed wiring, moisture-prone areas, overloading of circuits, and any other conditions that could pose a risk.
For example, if the environment is especially damp or prone to moisture, could voltage through components be reduced without impacting yield or efficiency? If so, using a grounded transformer could significantly reduce risk - to both those actively inspecting units, other staff and bystanders. By understanding these joint hazards and opportunities, engineers can prioritize corrective actions without compromising their safety.
Confirm equipment and supply are fit for purpose
Ensure that all electrical equipment is suitable for its intended purpose and is supplied with the appropriate electronic power source. This includes verifying voltage compatibility, circuit protection measures, and grounding systems. Any mismatch between equipment and power supply can lead to malfunction, overheating, or even electrical fires.
It’s important to consider the environment at large and not simply the panel itself when you ask ‘Is this safe?’ or ‘Is this fit for purpose’? Lateral, not linear, thinking is needed here. For example, if you are in a facility that has a potentially explosive atmosphere (such as a chemical distillery, mine or water processing plant) even the equipment used to inspect can itself pose a significant risk. You’ll need to apply for a Hot Work Permit to ensure the devices used to detect danger don’t inadvertently introduce it themselves. One way to circumvent this issue is to use safely encased, spark-proof inspection tools - such as the FLIR Cx5 thermal imaging camera suitable for ATEX rated hazardous environments.
Implement a Residual Current Device (RCD)
Installing a residual current device, such as a ground fault circuit interrupter (GFCI), is especially helpful while detecting abnormal currents and preventing electrical shocks as it can shut off electricity supplies in as little as 1/40 of a second. RCDs are much more sensitive than traditional fuses, giving you additional protection from electric shock and giving you valuable extra time to react should something be overlooked.
These devices quickly cut off power in the event of a ground fault, protecting personnel and equipment from potentially dangerous electrical currents. Of course, regular testing and maintenance of these devices are equally important to ensure their effectiveness.
Ensure users are properly trained
One of the fundamental aspects of electrical safety is ensuring that personnel are adequately trained and qualified to handle electrical equipment and perform tasks.
While your business should implement comprehensive training programs covering electrical safety protocols, emergency procedures, and proper use of personal protective equipment (PPE), it’s important to keep these current. Regulations are often updated as new information becomes available, and people understandably cannot retain information indefinitely. Regular refresher courses and competency assessments should be conducted to keep skills up to date, information relevant and staff always keeping safety in the forefront of their minds.
Similarly, some management decisions about maintenance can be made by individuals who don’t themselves have the relevant knowledge about electrical circuitry. If, for example, an operator is asked to inspect a unit urgently without the proper time to prepare or correct tools, refusing to comply and explaining the risk factors is imperative.
Fostering an open work environment in which operators can flag problematic instructions in favour of ensuring safety is vital. Does your company create such a culture?
Diagnose potential faults safely with FLIR thermography
A large part of detecting abnormalities in electrical panels within an electrical panel is the lack of visible components. Being housed behind plastic casing and protective tubing can make locating electrical faults difficult, especially in tight spaces.
Before any elements are handled, operators are advised to first inspect the entire electrical panel with a thermal imaging device. Thermography is a powerful tool for identifying potential electrical issues before they escalate into critical failures, enabling you to detect abnormal heat patterns from overheating elements, failing components or faulty connections. Timely intervention based on thermographic findings can prevent costly downtime, equipment damage, and safety hazards.
Thermal imaging cameras such as the FLIR ONE PRO, FLIR C5, FLIR E8 Pro or FLIR E6 Pro give unparalleled insight into what’s going on inside an electrical panel - without any need to contact individual elements. Compact thermal imaging cameras offer an ideal non-contact diagnostic tool for safely inspecting even the most challenging of units.
Safety is a mindset
Conducting safe electrical inspections is a responsibility that falls squarely on the shoulders of industrial engineers - but they must be supported by robust processes that mitigate risk and prioritise safety as a paramount concern.
By following a structured approach and utilizing the right tools and techniques, engineers can manage risk, ensure compliance with safety standards, and uphold the integrity of electrical systems within industrial environments. Remember, safety is not just a checklist; it's a mindset that should permeate every aspect of industrial operations.
Maintain operational integrity to safeguard production and prevent downtime - with acute thermal imaging insights from Teledyne FLIR. View the full range of FLIR electric condition monitoring equipment to transform your preventative maintenance routine today.