Driving crucial improvements: Why Europe’s largest rail network chooses thermography to ensure safe travel
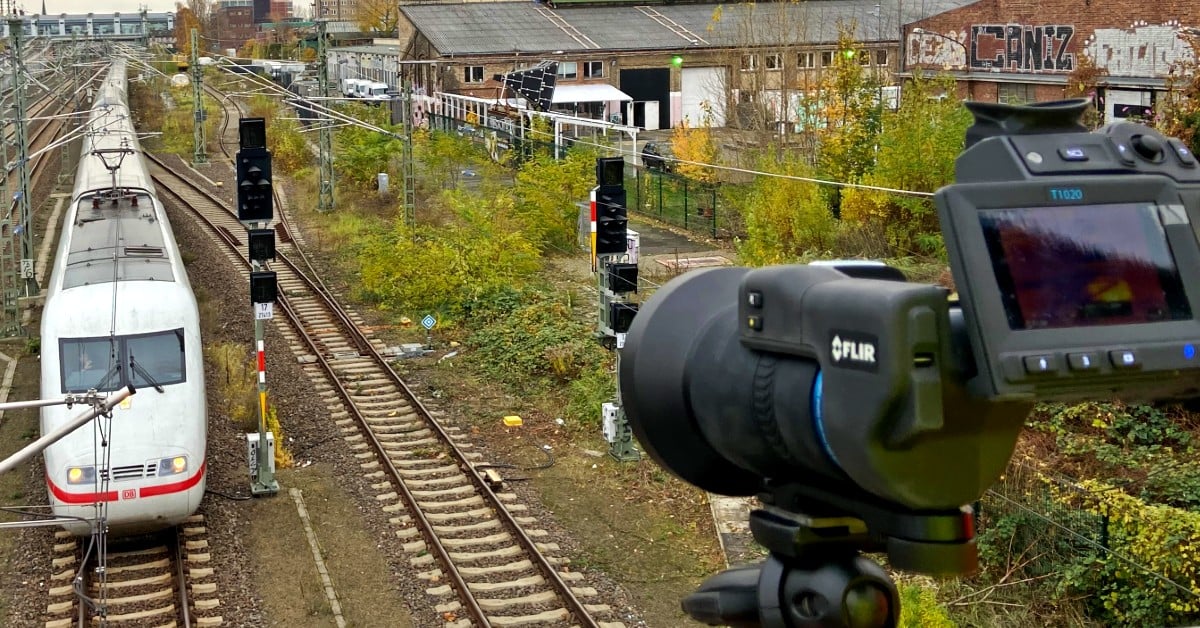
Passenger safety across the EU's rail network is consistently improving year on year, with almost a third fewer accidents in 2022 than in 2010, according to data from the ERA. Continued improvements to components, infrastructure and inspection methods no doubt play a critical role in driving this.
To protect its passengers, its cargo and its vital infrastructure, Deutsche Bahn equips its team with thermal imaging cameras to identify safety concerns on its almost 33,300 kilometers of track—Europe’s largest rail network.
The company has been using thermography for predictive and condition-based maintenance of its large network for 40 years, and leading the charge from DB Energie (as part of the “Technical Consulting East” department of the railway operator) is engineer Xiaoying Wang.
Xiaoying uses acute thermal insights to carefully inspect overhead lines, converters and converter stations for power anomalies or overheating components that could otherwise put the intricate network of tracks, and its users, at risk.
Thermography is “the only way” to find faults
Deutsche Bahn’s team of expert engineers must ensure their insights are as wide-ranging as its expansive infrastructure network, so it cannot rely solely on Xiaoying Wang and her small but impactful team.
Instead, the team uses a ‘divide and conquer’ approach, which consists of employees utilizing entry-level thermal imaging cameras (notably the FLIR E8 or FLIR ONE® Pro) to capture images of components they deem a concern. With clear images and a wealth of data available from these entry-level devices, Ms Wang can then remotely interpret the findings and offer relevant recommendations—or bring her trusty FLIR T1020sc with standard, wide-angle and telephoto lenses for more rigorous examinations.
A critical part of the inspection process is to coordinate with the central network office. This is vital to determine where on the extensive network of tracks the team should take readings and which precise elements they must monitor.
“Almost everything on the railway is designed for redundancy,” explains Ms Wang. “This ensures operations can continue to run smoothly even if a component fails. But it is precisely this redundancy that ensures that the components rarely reach their performance limits. If the technical service team wants to examine a specific component, they must ensure that the load is not distributed evenly across all parts of the system—as it typically would be—but mainly through the component under examination.
“This is the only way to use thermography to see whether everything is okay, or whether the component should be replaced immediately or at the next planned shutdown.”
While energy providers often use drones to inspect power lines, the load conditions on a Deutsche Bahn’s traction supply power line can change too rapidly. Inspections at speed would lack the required resolution to accurately examine components. To account for this, Ms Wang and her team plan a precise route, plot every junction and inspect manually in person. This could consist of as many as 30 nodes per route, each of which will require careful inspection on the track.
Current concerns: inspecting converters on the line
Another crucial element of the network inspected with thermography is converters and converter stations. This is critical because Deutsche Bahn’s fleet runs at a frequency of 16.7 Hertz, whereas the power grid operates at 50 Hertz.
Converter stations make the power a suitable voltage and avoid causing overheating components, electrical damage or fires. The stations consist of huge rotating pieces of machinery; the electric motor and generator alone can weigh up to 140 tonnes. This sturdy bit of kit converting electricity to a lower voltage can generate a significant amount of heat, so inspecting them with the FLIR T1020sc provides clear, crisp imagery of the internal elements and the heat emissivity of each component so that any wear, abnormalities or potential failures are addressed before they can worsen.
For safety reasons, in some converter plants, many control cabinets are now built in such a way that they can no longer be opened. To overcome this, Ms Wang uses a FLIR T1020 for semi-automated investigations, remotely operating a mobile robot to access maintenance of areas that are not accessible to humans.
Looking to the future: photovoltaics and thermal imaging
Deutsche Bahn has committed itself to the ambitious goal of becoming climate-neutral by 2040. The use of renewable energies and new technologies is a critical component of this.
To better research and test technologies and energy concepts under real conditions, Deutsche Bahn operates RealLabor Energy in Berlin. This is a carport equipped with PV modules and a “solar flower” which ensures part of the energy required is generated sustainably. The correct function can also be checked with FLIR thermal imaging camera; Ms Wang uses the FLIR T1020s with standard, wide-angle and telephoto lenses to generate high-resolution thermal images at a distance—which is vital to avoid arc flashes when inspecting in a high-voltage area—and up close, for control cabinets to ensure every element is included in the field of view.
Training and support from a Teledyne-FLIR integrator
Offering vital insights into FLIR technology and its most impactful applications is Teledyne-FLIR integrator Rolf Weber Group.
Andreas Blug from the Rolf Weber Group said “It is necessary not only to provide employees with thermal imaging cameras but also to train them in their use. This is the only way to create meaningful thermograms.”