Improving quality in heated windscreen production through a turnkey imaging solution with thermography
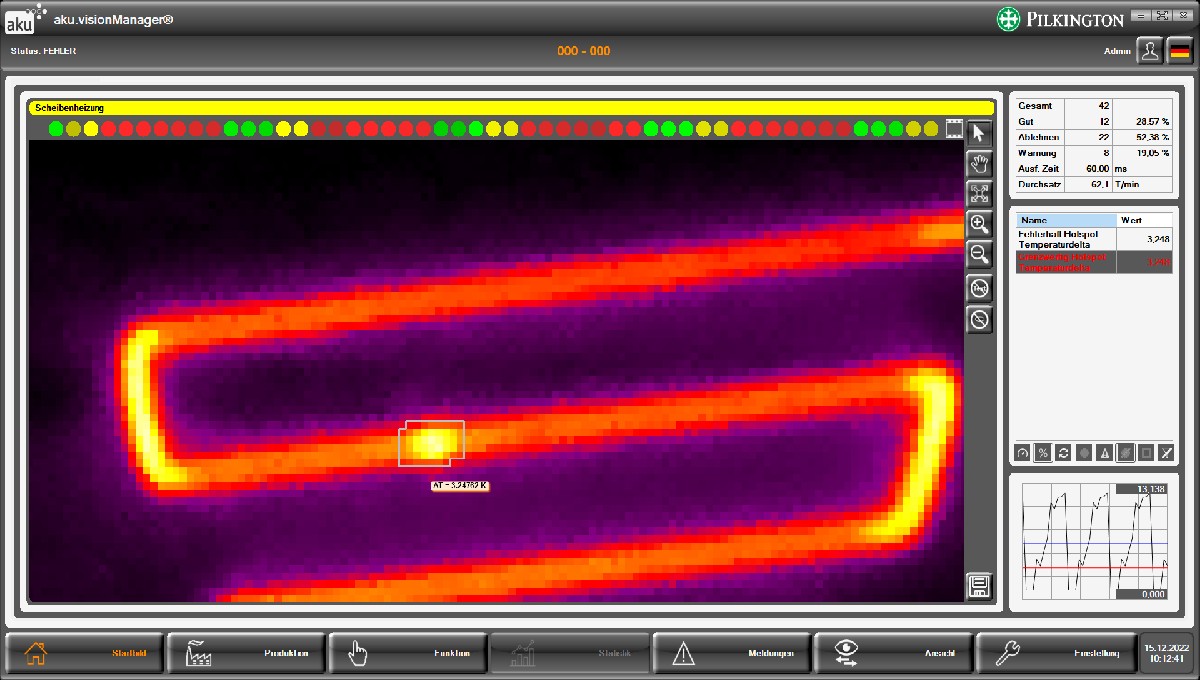
In the world of high-end car production, any issues with quality or performance can seriously impact profit and reputation. When consumers are paying a premium price, they expect the car to match the price tag.
A German integrator called aku.automation was recently tasked with developing a quality inspection system for heated car windscreens for one of the world’s premium car brands.
Using FLIR thermal imaging cameras, alongside PCs running bespoke software, aku.automation designed and built a complete solution, ensuring consistent quality and preventing costly recalls.
Using thermal imaging to inspect printed circuits
aku.automation’s customer, Pilkington Automotive, is part of NSG Group and one of world’s leading manufacturer of glass and glazing products, supplying heated windscreens to all major car manufacturers worldwide. The company used to perform manual quality checks on every product, but was looking for an advanced quality testing system to further optimize quality performance.
Pilkington Automotive's brief to the specialist in the field of machine vision, aku.automation, was to detect hot spots on printed circuits within the windscreens that form the heating system. A hot spot indicates that the heating system is faulty and may not work properly once installed.
aku.automation sent a technical team to the Pilkington Automotive plant to set up a small test system that allowed the team to capture production line images to ensure the application would work. After a successful test result, aku.automation presented their solution.
Spotting defects effectively and improving quality
The solution involved installing a FLIR A70 camera above the production line and linking to a PC running the aku.visionManager® software. This system allows the integration of manufacturer-independent libraries, components and interfaces and thus offers a uniform operating concept that ensures the greatest possible time and cost savings. aku.visionManager processes the data and displays the resulting thermal images with error graphics on a monitor for operators to inspect.
A small amount of voltage is run through the circuits while the images are captured. If the heating system is working as it should, the circuit will be illuminated evenly. However, if the circuit is faulty, a hot spot will appear on the thermal image.
Any defective windscreens can be easily identified and removed from the line. In addition, the error pattern can be analyzed in order to further optimize the production process in the future.
The FLIR A70 thermal camera that aku.automation selected features MSX® image enhancement, radiometric data transmission over Wi-Fi, and a close up lens for accurate thermal measurements, even on small components. The inspection area is located at the upper edge of the windscreen in the mounting area of the rear-view mirror, so aku.automation chose a close-up 29° lens for the A70 that is ideal for measuring a relatively small area.
And with a 640×480 pixel detector—the highest thermal resolution of any fixed mount camera in the FLIR A50/A70 camera range—it gave operators a clear picture of potential defects.
Providing solutions in partnership
To find the right solution to its quality control issue, Pilkington Automotive first approached FLIR, who brought in their trusted German automation partner, aku.automation, for support.
Martin Stengel, Sales Manager at AKU, said: “FLIR has the expertise when it comes to the camera itself, and we know how to implement an automatic inspection system with image processing algorithms. After extensive research, we offered a complete solution and Pilkington Automotive ordered it. At the beginning of last year we started to implement and test the system. Today, the system runs in production and the customer is satisfied and everything works as expected."
“We have a partner agreement with FLIR. This means they pass on requests to companies like us to provide solutions in the industrial automation environment. We’ve done this for three or four years. Thermal imaging cameras are currently not our main business, but we are seeing more and more interesting applications in this area. We look forward to implementing similar projects like this in close cooperation with FLIR in the future.”